德國進口WAGO 750-468模塊的技術參數(shù),工作原理如下。
在精密機械加工領域,WAGO 750-468 模塊憑借其出色的信號采集與處理能力,成為保障加工精度的核心組件。該模塊支持 8 路模擬量輸入,可直接對接光柵尺、激光干涉儀等高精度測量設備,將微米級的位移信號轉化為數(shù)字信號,為數(shù)控系統(tǒng)提供實時反饋。例如,在精密齒輪磨削過程中,齒輪的齒距誤差需控制在 3μm 以內,模塊通過采集光柵尺傳來的位置信號,實時計算砂輪與工件的相對位移,當檢測到偏差超過 0.5μm 時,立即觸發(fā)數(shù)控系統(tǒng)的補償指令,調整砂輪進給量,確保齒面精度符合設計標準。其 16 位分辨率配合 ±0.1% 的測量精度,即使在高速切削(主軸轉速達 15000r/min)時,仍能穩(wěn)定捕捉微小的振動信號,避免因刀具顫振導致的表面粗糙度超差,使工件表面光潔度保持在 Ra0.02μm 級別。

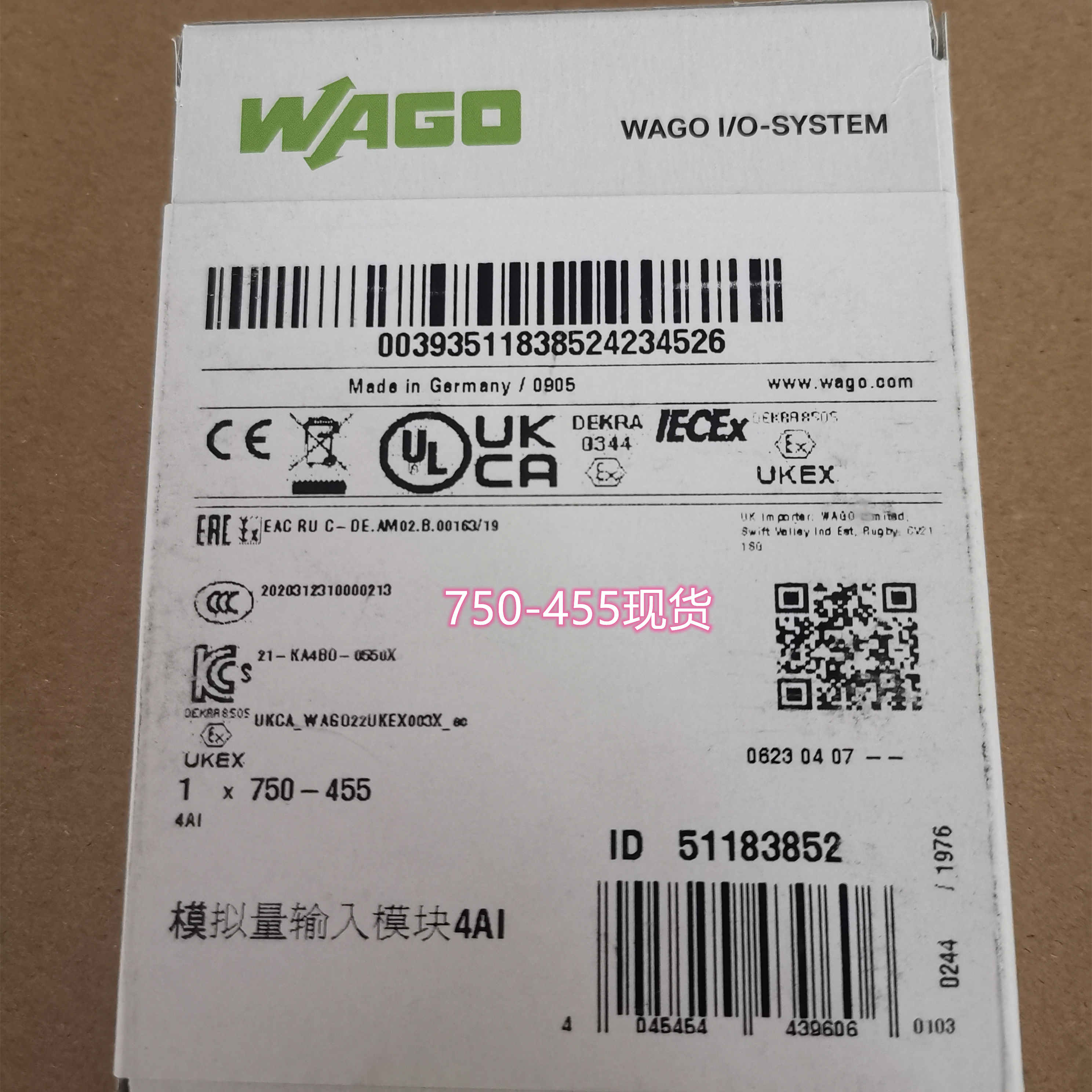
同時,模塊的抗干擾設計在精密機械車間發(fā)揮關鍵作用。車間內多臺數(shù)控機床同時運作時,高頻電機與變頻器會產生強烈電磁干擾,而 WAGO 750-468 模塊采用光電隔離技術,將輸入信號與系統(tǒng)電路隔離,共模抑制比達 120dB,確保在 10V/m 的電磁環(huán)境中,測量誤差不超過 0.3μm。在航空發(fā)動機葉片的五軸加工中,模塊同步采集溫度傳感器的信號,當環(huán)境溫度變化超過 ±1℃時,自動修正熱變形誤差,使葉片型面加工精度維持在 5μm 以內,滿足航空級零部件的嚴苛要求。通過與 MES 系統(tǒng)聯(lián)動,模塊還能記錄每批次工件的加工參數(shù),為質量追溯提供完整數(shù)據(jù)鏈,當出現(xiàn)尺寸偏差時,可快速定位到刀具磨損或夾具松動等原因,將返工率降低至 0.5% 以下。
在精密設備的協(xié)同運作中,WAGO 750-468 模塊的高速數(shù)據(jù)傳輸能力為生產線的智能化調度提供支撐。模塊化設計使其可靈活接入工業(yè)以太網(wǎng),通過 PROFINET 協(xié)議實現(xiàn)與機器人、上下料設備的實時通信,數(shù)據(jù)更新周期僅為 250μs,確保多設備聯(lián)動誤差控制在 1ms 以內。例如,在半導體封裝設備的晶圓搬運環(huán)節(jié),模塊采集機械臂末端的真空壓力信號(范圍 - 100kPa 至 0),當壓力波動超過 ±2kPa 時,立即暫停搬運動作并觸發(fā)報警,避免晶圓因吸附不穩(wěn)導致的碎裂,將良品率提升至 99.9%。其支持的熱插拔功能允許在不停機狀態(tài)下更換模塊,配合冗余電源設計,使設備平均運行時間(MTBF)延長至 80000 小時,滿足半導體行業(yè) 24 小時連續(xù)生產的需求。
此外,在精密計量儀器的校準流程中,模塊的高精度特性保障了量值傳遞的準確性。三坐標測量機在檢測精密模具時,需通過模塊采集測頭的力反饋信號(范圍 0-10N),當接觸力超過 3N 時自動切換測量速度,避免壓傷模具表面的微米級紋路。模塊將力信號轉化為數(shù)字量后,與激光干涉儀的位置數(shù)據(jù)融合計算,生成三維誤差補償模型,使測量機的空間精度從 2.5μm/m 提升至 1.8μm/m。在醫(yī)療設備的零件加工中,如人工關節(jié)的鈦合金假體磨削,模塊實時監(jiān)測冷卻液的流量與溫度,當流量低于 5L/min 或溫度超過 30℃時,自動調節(jié)冷卻系統(tǒng),防止因熱變形導致的假體球面度誤差超標,確保植入體與人體骨骼的貼合度達到 99% 以上
WAGO 750-1400
萬可750-1500
進口模塊750-455